Swissmem features ESPROS in its Involved magazine
The following is a translation of the original German text.
Top end technology instead of dusty tunnels: ESPROS Photonics AG manufactures highly sensitive microchips in Sargans – primarily underground. The clean room in the rock protects the sensitive production from vibrations and dirt. In addition to historic mines, tomorrow’s markets are being co-developed inside the Gonzen mountain.
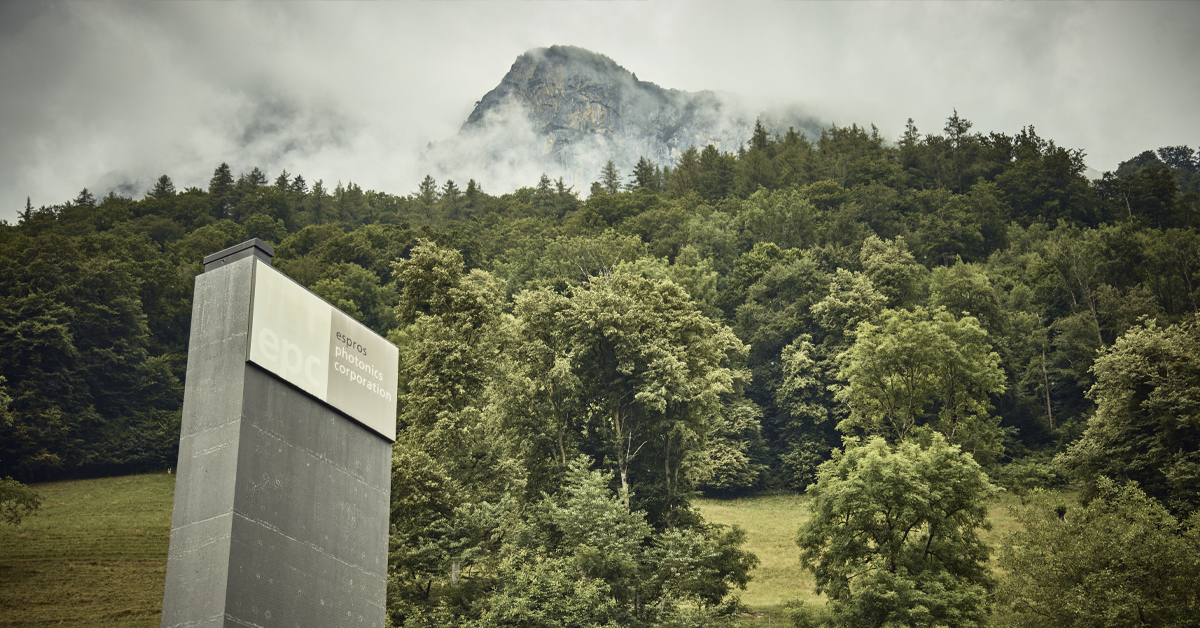
Image: © Christian Grund
Like the rings of a puddle into which a pebble has been thrown – that’s how vibration spreads out here in the alluvial plain between the Rhine and Lake Walen (Walensee). The ground around Sargans is soft and in motion: when a train glides over rails, when a lorry crashes over roads. “That’s why we went into the rock,” explains Beat De Coi. “Our clean room is surrounded by solid rock. Mount Gonzen is our foundation, our façade, our roof. A protective wall against the smallest vibrations.”
The CEO of ESPROS Photonics AG speaks in colorful pictures. Fortunately! He is used to making his complex subject understandable to laypeople: the semiconductor industry. Microchips. In his case: for 3D cameras. But actually no digital device today can do without chips. They perform control, storage and computing tasks. Despite this, hardly anyone understands what the technology is actually about.
De Coi is patient: ESPROS manufactures highly sensitive microchips that are usually only 50 micrometers thick. There are around 30,000 individual chips on a wafer, a 20-centimeter diameter silicon disc coated with photoresist. The production of a wafer costs several thousand francs. To separate the chips, wafers are sawn up at the end. The entire manufacturing process is delicate. This is because wafers are exposed to ultraviolet light via a photomask between many other steps. The mask has structures that are only a few hundred nanometers in size. For comparison: one nanometer is about as big as a fingernail grows per second. These tiny structures must be transferred to the silicon wafer without distortion. If even the slightest vibration occurs during this process, they “smear”. The semiconductor chip then loses its function. As you can imagine, only a few people were able to produce chips.
A daring project
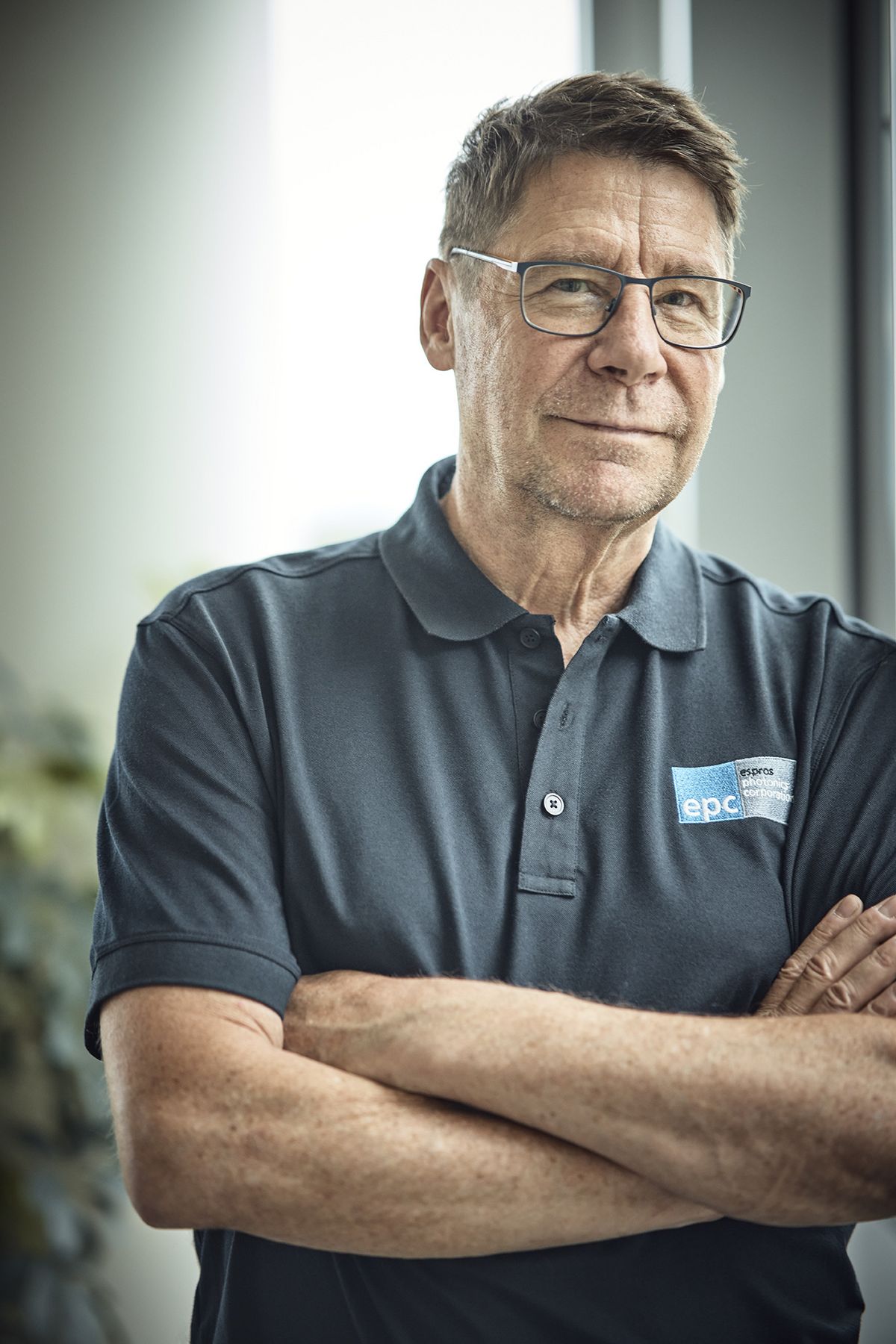
Visionary, founder and CEO Beat De Coi (Image © Christian Grund)
This is precisely why De Coi’s company was founded. “As an electronics engineer, I have been involved in sensor technology since the 1980s. I founded CEDES AG and we grew to 500 employees to develop special optical sensors for lifts. However, I was unable to implement many of my ideas because there was simply a lack of suitable semiconductor chips.” So – it sounds crazy – he took the reins himself in 2005. De Coi made plans to build his own semiconductor factory. But what would he actually need for such an undertaking? De Coi researched, read technical literature, immersed himself in semiconductor physics and obtained expertise. The detailed planning shows: He had to reckon with investment costs of around 160 million francs. The planned factory would need the energy of a village with two thousand inhabitants. And: access to large quantities of cooling water. The requirements are high. He thinks to himself: “In the rock, that’s where we should be!
We are allowed in
Warning and prohibition signs are attached to the doors. Only trained employees are allowed to enter the two cleanrooms. Hood, face mask, overalls, overshoes and gloves: the airlock can only be entered with cleanroom clothing, as highly toxic gases and acids are used in chip production. At the same time, discipline is required to avoid contamination. “Even skin flakes would damage the wafer. Then the value of a small car is gone,” says the owner. A class 100 clean room is required for production, which means that a maximum of 100 dust particles per 30 liters of air is acceptable. In Sarganserland, there are normally 100,000 or more dust particles per 30 liters of air. When the foehn wind from the south,blows down the Rhine Valley, it can be as high as 500,000. There are far fewer whirring around underground, which takes the strain off the filters. Another advantage of underground rooms is that the temperature remains relatively stable. In production, it has to be controlled to within a tenth of a degree and the humidity to within a few percent; day and night, summer and winter. The rock therefore helps to save energy and costs.
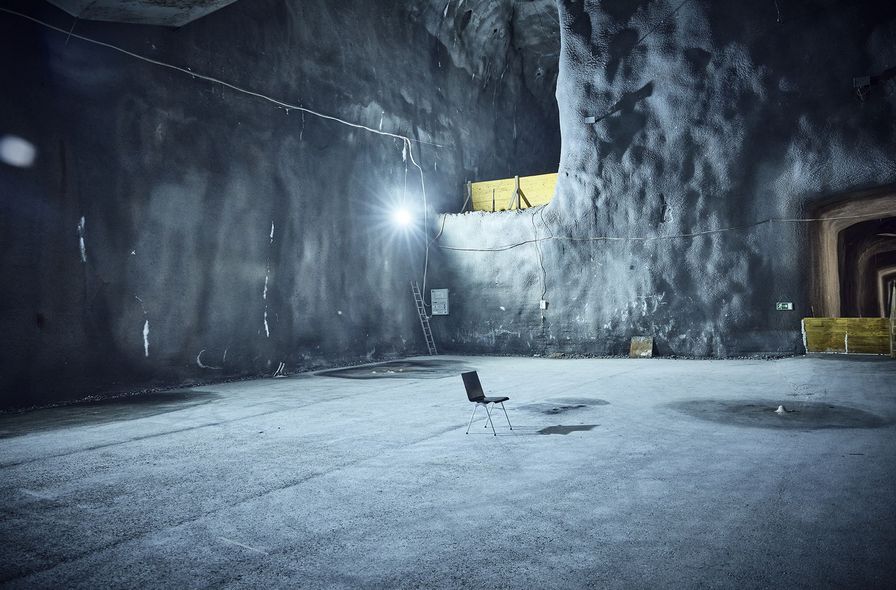
One of many caverns? Ore was mined in Gonzen until the 1960s. The pits perforate the massif for 90 kilometers. But this cave was blown out of the mountain for ESPROS. The company carries out tests here. (Image: ©Christian Grund)
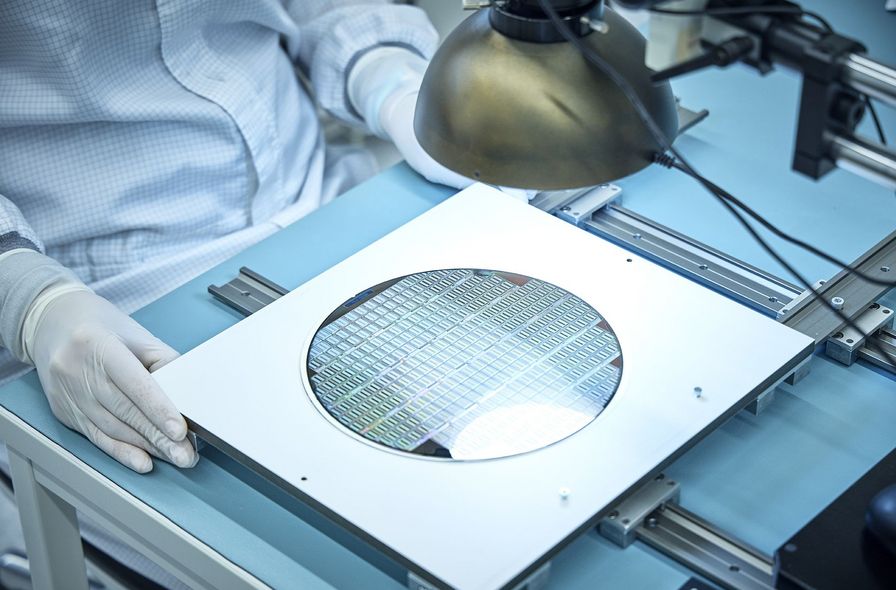
A wafer is worth several thousand francs and is extremely sensitive. Around 30,000 chips are arranged on it, which will later be broken out. (Foto: ©Christian Grund) (Image: ©Christian Grund)
Unrivaled worldwide
The total investment in research, technology development, buildings and infrastructure ultimately amounted to around CHF 100 million. It was financed entirely by private funds without subsidies. As a result, there is now a semiconductor manufacturer in Eastern Switzerland with a technology that is unique in the world.
You have to know: Most chips are manufactured in Asia, for example in Taiwan or China. Production is cheaper there. ESPROS Photonics AG from Sargans is an exception. However, relocating production is out of the question. Beat De Coi says: “I am a Swiss entrepreneur and I am convinced that we can do the same here. It is important to me to create jobs in the region. But to keep up, you need innovation.” The clean room in the rock is also patented. And ESPROS’ technology is unrivaled worldwide. This mainly concerns the fact that the optical sensors, the chips, always work equally well almost regardless of the ambient light – be it in the dark of night or in full sunshine. This is important because 3D cameras with ESPROS sensors are in use day and night, often very close to people: they give autonomous vehicles and logistics robots their “eyesight”, so to speak, and help with orientation. Or support night-time monitoring in care homes and hospitals. If something goes wrong, it can quickly become dangerous.
“A large corporation would never have done what we have developed. The investments would have been too large, with a high risk of going nowhere. It took perseverance, courage and entrepreneurial spirit.”
-Beat De Coi CEO of ESPROS Photonics AG
The sensors use particles of light, photons, to measure distances. They therefore recognize how far away objects are and where they are in space. Put simply, if a photon takes a long time to travel back and forth from the camera in the autonomous vehicle to the sign in the parking lot, the distance is great. If the photon takes a shorter time, the car should stop so that it does not cause an accident. The technical problem here is that the photons from the camera flash cannot be distinguished from those from the sun. If the sun is shining brightly, the distance measurement is disturbed because all the light is streaming into the camera. So how do you filter out the relevant photons? This is the company’s unique secret recipe. “Our trick: we have developed a technology that allows us to manipulate charges in the semiconductor. We add and subtract photons and can therefore always measure distances accurately,” says the entrepreneur. “A large corporation would never have done what we developed. The investment would have been too large, with a high risk that it would not lead anywhere. It took perseverance, courage and entrepreneurial spirit.” And vision: Beat De Coi already believed in autonomous vehicles as a student, when there were as yet no cell phones. And dedicated his career to markets that most people only knew from science fiction films.
Where does the visionary see the next big thing? “We will compensate for the shortage of skilled workers thanks to technology,” he is convinced. “We will continue to automate tasks in care, catering and in the municipalities.” Of course, he is already working on this huge trend: Equipping sensors with artificial intelligence (AI). With his technology, residents’ falls in care homes can be detected via 3D camera images, evaluated using AI and an alarm triggered. Pushing the boundaries of the imaginable – that’s how Beat De Coi lives and thinks. Even if it means blasting a hole in the rock.
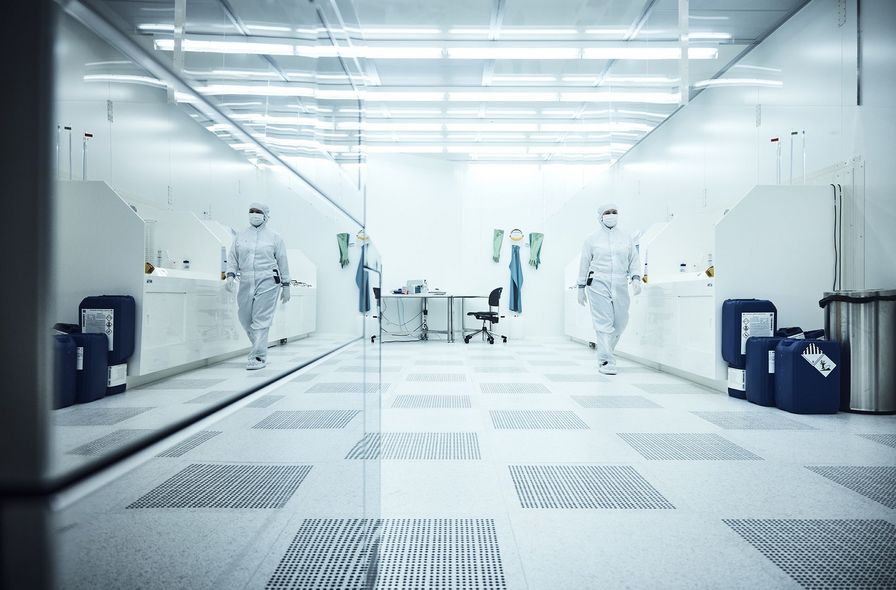
The clean rooms are partially built into the rock to reduce dust particles, temperature fluctuations and vibration. (Image: ©Christian Grund)
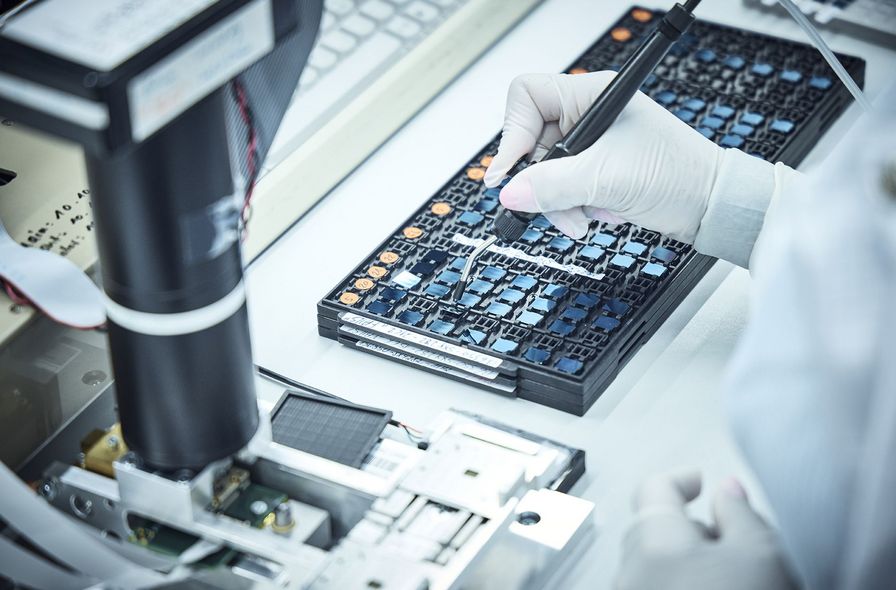
The final inspection involves testing again. Are all chips working properly? (Image: ©Christian Grund)